US Manufacturing Automation: Job Role Impacts by 2025
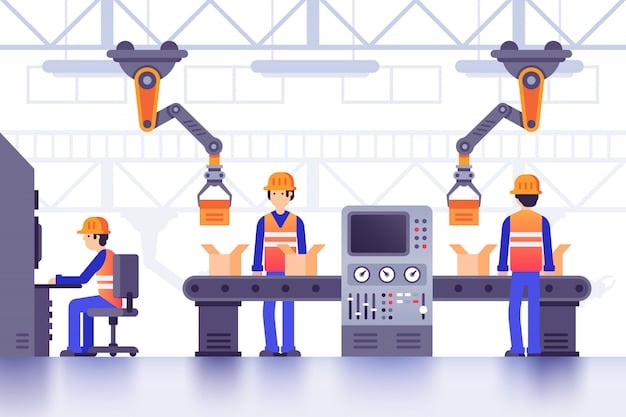
The projected 12% increase in US manufacturing automation by 2025 is expected to significantly reshape job roles, leading to a demand for new skills in areas like robotics maintenance and data analysis, while also potentially displacing workers in routine manual tasks.
The US manufacturing sector is on the cusp of a significant transformation. The projected 12% increase in US manufacturing automation by 2025 signals a shift in required skills and potential job displacement.
Understanding the Automation Surge in US Manufacturing
Automation is no longer a futuristic concept; it’s a present-day reality rapidly reshaping industries worldwide, and the US manufacturing sector is no exception. Understanding the drivers behind this surge is crucial to anticipate its wide-ranging effects.
Economic Drivers of Automation
Several economic factors are fueling the increasing adoption of automation. These include the desire to increase productivity, reduce costs, and improve overall efficiency in manufacturing processes.
Technological Advancements
Significant technological advancements have made automation more accessible and effective. Innovations in robotics, artificial intelligence (AI), and machine learning are driving the development of more sophisticated and versatile automated systems.
- Cost Reduction: Automation can significantly reduce labor costs, particularly in repetitive or physically demanding tasks.
- Increased Productivity: Automated systems can operate continuously, leading to higher output and faster production cycles.
- Improved Quality: Automation reduces the risk of human error, resulting in more consistent and higher-quality products.
The convergence of these economic and technological forces is creating a powerful incentive for US manufacturers to invest in automation, promising significant returns and competitive advantages.
The Evolving Landscape of Manufacturing Job Roles
As automation becomes further integrated into manufacturing processes, the nature of job roles is undergoing a profound transformation. This evolution presents both challenges and opportunities for the workforce.
Decline in Repetitive Manual Labor
Many traditional manufacturing jobs that involve repetitive manual labor are likely to be phased out as automated systems take over these tasks. This trend will require workers to transition to new roles or acquire new skills.
Rise of Technical and Managerial Positions
While some jobs may be eliminated, automation is also creating new opportunities in technical and managerial roles. These positions involve designing, implementing, maintaining, and overseeing automated systems.
- Robotics Technicians: Skilled professionals who install, maintain, and repair robotic systems.
- Automation Engineers: Engineers who design and implement automated manufacturing processes.
- Data Analysts: Experts who analyze data generated by automated systems to optimize performance and identify areas for improvement.
This shift signifies a move towards a more skilled workforce, where technical expertise and problem-solving abilities are highly valued.
Skill Gap and the Need for Workforce Development
One of the biggest challenges arising from increased automation is the widening skill gap. Many workers lack the necessary skills to operate and maintain automated systems effectively.
Identifying Skill Deficiencies
Assessing the existing skill gaps is crucial to develop targeted training programs. This assessment should cover technical skills, such as programming and maintenance, as well as soft skills, such as problem-solving and critical thinking.
Investing in Training and Education Programs
Closing the skill gap requires significant investment in training and education programs. These programs should be designed to equip workers with the skills they need to succeed in an automated manufacturing environment.
- Apprenticeships: Programs that combine on-the-job training with classroom instruction.
- Vocational Training: Courses that provide hands-on training in specific technical skills.
- Online Courses: Accessible and flexible learning options for workers to upgrade their skills.
By addressing the skill gap proactively, the US can ensure that its workforce is prepared to embrace the opportunities created by manufacturing automation.
Impact on Wages and Income Inequality
The rise of automation has significant implications for wages and income inequality in the manufacturing sector. Understanding these impacts is essential to develop policies that promote equitable economic growth.
Potential for Wage Stagnation and Decline
The displacement of workers in low-skilled jobs could lead to wage stagnation or decline for those who are unable to transition to higher-skilled roles. This trend could exacerbate income inequality.
Opportunities for Wage Growth in Skilled Positions
On the other hand, the demand for skilled workers in technical and managerial positions could drive wage growth in these areas. This could create new opportunities for upward mobility for workers who acquire the necessary skills.
Addressing the potential negative impacts on wages requires policies that support workforce development, promote fair labor practices, and ensure that the benefits of automation are shared more broadly.
Policy and Regulatory Considerations
Governments and regulatory bodies play a crucial role in shaping the future of manufacturing automation. Thoughtful policies can help mitigate the negative consequences of automation and maximize its benefits.
Incentivizing Investment in Workforce Development
Governments can provide tax incentives, grants, and other forms of support to encourage manufacturers to invest in workforce development programs. This can help ensure that workers have access to the training they need to succeed in an automated environment.
Strengthening Social Safety Nets
Expanding social safety nets, such as unemployment insurance and retraining programs, can provide a cushion for workers who are displaced by automation. These programs can help workers transition to new jobs and acquire new skills.
- Tax Credits for Training: Encouraging companies to invest in employee training.
- Unemployment Benefits: Providing financial support to displaced workers.
- Investment in Education: Supporting educational institutions to offer relevant training programs.
Proactive policies are essential to ensure that automation leads to inclusive economic growth and benefits society as a whole.
Preparing for the Future: Strategies for Workers and Businesses
To thrive in the age of manufacturing automation, both workers and businesses need to adopt proactive strategies. These strategies should focus on adaptability, continuous learning, and innovation.
For Workers: Embrace Continuous Learning
Workers should embrace a mindset of continuous learning and be prepared to acquire new skills throughout their careers. This may involve taking online courses, attending workshops, or pursuing formal education.
For Businesses: Invest in Technology and Talent
Businesses should invest in both technology and talent. This includes not only adopting automated systems but also developing the workforce necessary to operate and maintain them effectively.
- Upskilling Programs: Offering training to existing employees to adapt to new technologies.
- Partnerships with Education Institutions: Collaborating to create relevant training programs.
- Creating a Culture of Innovation: Encouraging employees to develop new ideas and solutions.
By embracing these strategies, workers and businesses can position themselves for success in the evolving manufacturing landscape.
Key Point | Brief Description |
---|---|
🤖 Automation Growth | Projected 12% increase in US manufacturing by 2025. |
🛠️ Job Role Changes | Decline in manual labor; rise in technical and managerial roles. |
🎓 Skill Gap | Need for workforce development in robotics, AI, and data analysis. |
💰 Wage Impact | Potential wage stagnation for low-skilled workers, growth in skilled positions. |
FAQ
▼
Automation may lead to job displacement in manual roles, but it also creates new opportunities in technical areas. Continuous learning and adaptation are crucial for job security.
▼
Skills in robotics maintenance, programming, data analysis, and automation engineering will be highly sought after. Soft skills like problem-solving are also essential.
▼
Businesses should invest in upskilling programs, partner with educational institutions, and create a culture of innovation to prepare their workforce effectively.
▼
Government can incentivize workforce development, strengthen social safety nets, and promote policies that ensure the benefits of automation are shared broadly to benefit all.
▼
Workers should embrace continuous learning, acquire new skills, and be adaptable to changing job roles. Online courses and vocational training are excellent resources.
Conclusion
The projected increase in US manufacturing automation by 2025 presents both challenges and opportunities. By understanding the evolving job landscape, addressing the skill gap, and implementing proactive strategies, the US can ensure that automation leads to a more prosperous and equitable future for all.