The Future of Robotics in US Manufacturing: 5-Year Predictions
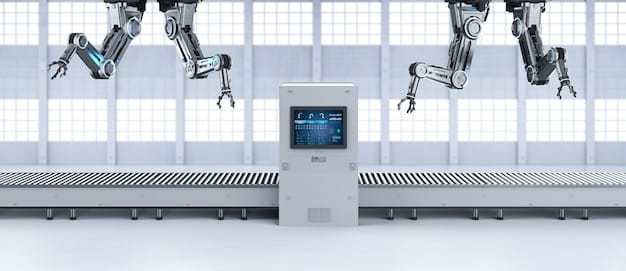
The future of robotics in US manufacturing over the next five years is poised for significant growth, driven by advancements in AI, increasing automation demands, and the need for enhanced efficiency and resilience in supply chains, leading to smarter, more collaborative, and adaptable robotic systems.
The landscape of US manufacturing is on the cusp of a robotic revolution. The next five years promise a transformation driven by technological advancements, economic pressures, and a growing recognition of the strategic importance of automation. This article delves into the future of robotics in US manufacturing: predictions for the next 5 years, exploring the key trends and innovations that will shape the industry.
Robotics Adoption: An Upward Trajectory
The adoption of robotics in US manufacturing is not a new phenomenon, but its pace and scope are set to accelerate dramatically. Factors such as labor shortages, the desire to reshore manufacturing operations, and the increasing affordability of robotic systems are driving this trend.
Key Drivers of Robotics Adoption
Several factors are converging to create a perfect storm for robotics adoption in US manufacturing. These include:
- Labor Shortages: A persistent shortage of skilled labor is forcing manufacturers to turn to automation to fill critical roles.
- Reshoring Initiatives: Efforts to bring manufacturing back to the US are fueled by automation, which can make domestic production more cost-competitive.
- Cost-Effectiveness: The cost of robotic systems has decreased significantly in recent years, making them more accessible to a wider range of manufacturers.
The Impact on Productivity and Efficiency
Robotics are not just about replacing human workers; they are about augmenting their capabilities and creating smarter, more efficient manufacturing processes. The implementation of robotic systems is leading to significant improvements in productivity, quality, and overall efficiency.
The utilization of robotics translates into a considerable enhancement of productivity, refinement of product quality, and streamlining of overall operational efficacy. As the technology develops, the implementation of robotics promises to facilitate even greater degrees of optimization and efficiency throughout the industrial sector.
In conclusion, the increasing adoption of robotics in US manufacturing is poised to reshape the industry landscape, driven by a confluence of economic, technological, and strategic factors. This will lead to more resilient and competitive manufacturing operations.
AI-Powered Robotics: The Next Frontier
The integration of artificial intelligence (AI) into robotics is unlocking new possibilities for automation in manufacturing. AI-powered robots can perform more complex tasks, adapt to changing conditions, and learn from their experiences.
Advancements in Machine Learning
Machine learning algorithms are enabling robots to analyze vast amounts of data, identify patterns, and make informed decisions without explicit programming. This is particularly valuable in dynamic manufacturing environments where conditions can change rapidly.
- Predictive Maintenance: AI algorithms can analyze sensor data from robots to predict when maintenance is needed, reducing downtime and improving overall equipment effectiveness.
- Quality Control: AI-powered vision systems can inspect products for defects with greater accuracy and speed than human inspectors.
- Process Optimization: AI algorithms can analyze manufacturing processes to identify bottlenecks and optimize workflows for maximum efficiency.
The Rise of Cognitive Robotics
Cognitive robotics aims to create robots that can understand and reason about their environment, allowing them to perform more complex tasks and collaborate more effectively with human workers. This involves integrating AI with advanced sensors, computer vision, and natural language processing.
Cognitive robotics is rapidly transforming several sectors through the implementation of computer vision and natural language processing. These developments collectively facilitate robots in acquiring a more profound insight into their surroundings, thereby enabling these automated systems to undertake more intricate responsibilities and to function in close collaboration with human counterparts.
In conclusion, the fusion of AI and robotics is ushering in a new era of intelligent automation in US manufacturing. This will lead to more flexible, adaptable, and efficient manufacturing processes.
Collaborative Robots (Cobots): A Human-Centered Approach
Collaborative robots, or cobots, are designed to work alongside human workers, rather than replacing them. Cobots are equipped with advanced sensors and safety features that allow them to operate safely in close proximity to humans.
Benefits of Cobots in Manufacturing
Cobots offer several advantages for manufacturers, including:
- Increased Flexibility: Cobots can be easily reprogrammed and redeployed to perform different tasks, making them ideal for manufacturers with diverse product lines.
- Improved Safety: Cobots are designed with safety in mind and can operate safely alongside human workers.
- Enhanced Productivity: Cobots can automate repetitive or physically demanding tasks, freeing up human workers to focus on more complex and creative activities.
Applications of Cobots in Various Industries
Cobots are finding applications in various industries, including:
Automotive industry: Cobots engage in performing tasks such as the installation of components, precision welding, and the conduct of quality assessments.
Aerospace Industry: Cobots assist in composite material assembly, inspection operations, and fastening applications.
Electronics Industry: Cobots prove indispensable in handling delicate components, assembling intricate electronic devices, and executing testing protocols.
As cobot technology advances, their versatility, security features, and ease of integration are making them progressively appealing to organizations across a wide spectrum of manufacturing domains.
In conclusion, cobots represent a human-centered approach to automation, enhancing the capabilities of human workers and creating more collaborative and efficient manufacturing environments.
Robotics in Supply Chain Management: Building Resilience
Robotics are playing an increasingly important role in supply chain management, helping manufacturers to improve efficiency, reduce costs, and build resilience in the face of disruptions.
Automation of Warehouse Operations
Robots are automating various warehouse operations, including:
- Order Fulfillment: Robots can pick, pack, and ship orders with greater speed and accuracy than human workers.
- Inventory Management: Robots can track inventory levels and optimize storage locations to maximize efficiency.
- Materials Handling: Robots can transport materials throughout the warehouse, reducing manual labor and improving safety.
Enhancing Logistics and Distribution
Furthermore, robotics technology is undergoing a transformation that is streamlining logistics and distribution operations across the supply chain. Robotics-driven conveyance vehicles, along with autonomous trucks, are being leveraged to enhance the efficacy and reliability of product transport. These advancements not only facilitate faster delivery timelines but also diminish the likelihood of human-induced errors.
Robotics-guided logistics and distribution have proven indispensable in surmounting the obstacles intrinsic to advanced supply chains. Through automated operations, organizations can attain heightened efficacy, enhanced reliability, and elevated levels of resilience in meeting customer demands.
In conclusion, robotics are providing manufacturers with the tools they need to build more resilient and efficient supply chains, enabling them to respond quickly to changing market conditions and customer demands.
Challenges and Opportunities in Robotics Deployment
While the future of robotics in US manufacturing is bright, there are several challenges that manufacturers must address in order to successfully deploy robotic systems.
Addressing Skills Gap and Workforce Training
One of the biggest challenges is the skills gap. Manufacturers need workers who can program, operate, and maintain robotic systems. This requires investing in workforce training programs and partnerships with educational institutions.
Overcoming Integration and Interoperability Issues
Integrating robotic systems with existing manufacturing equipment and software can be complex and costly. Manufacturers need to adopt open standards and invest in interoperability solutions to ensure that their robotic systems can communicate and work together seamlessly.
Ethical frameworks for robotics
Beyond technological considerations, it is imperative that society deals with the implementation of robotics through thoughtful ethical structures. As robots are increasingly integrated into manufacturing, a careful evaluation of the impacts on labor, the potential for bias in AI algorithms, and the responsibility for robot-driven decisions becomes essential.
These structures are critical for ensuring that robotics enhance human welfare and are utilized in accordance with principles of fairness and openness within the ever changing environment of manufacturing.
Key Point | Brief Description |
---|---|
🤖 Robotics Adoption | Increasing due to labor shortages and reshoring. |
🧠 AI-Powered Robotics | Enhances decision-making and process optimization. |
🤝 Collaborative Robots | Works alongside humans, increasing flexibility and safety. |
🚚 Supply Chain Robotics | Improves warehouse operations and logistics. |
FAQ
▼
Robotics will introduce greater automation and efficiency. Tasks can be performed faster and more accurately, reducing costs and improving product quality. Also it is expected to reshape workforce requirements.
▼
Robots can work continuously without breaks, perform dangerous tasks, and increase productivity. They also ensure consistent quality, reduce waste, and improve overall operational efficiency.
▼
Collaborative robots (cobots) enhance human capabilities. Cobots take over repetitive tasks, while human workers focus on complex problem-solving, innovative tasks, and creative projects,
▼
Challenges include high initial costs, the need for a skilled workforce, and integrating robots with existing systems. It’s essential to address such issues effectively for smooth deployment.
▼
Manufacturers can prepare by investing in workforce training, modernizing the IT infrastructure, and performing process analysis. It is also important to assess the potential for robots in their workflow.
Conclusion
In conclusion, the next five years will be a period of rapid transformation for US manufacturing, driven by the adoption of robotics and automation. By embracing these technologies and addressing the associated challenges, manufacturers can unlock new levels of efficiency, productivity, and competitiveness, ensuring a strong and vibrant future for the industry.