US Manufacturing Automation: Job Creation Impact by 2025
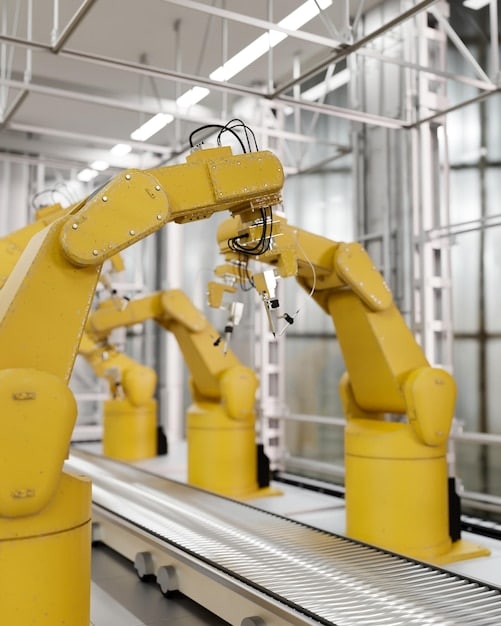
The projected 12% increase in US manufacturing automation by 2025 is expected to reshape the job market, creating new roles in technology and management while potentially displacing workers in routine tasks, necessitating strategic workforce adaptation and retraining initiatives.
How will the projected 12% increase in US manufacturing automation impact job creation by 2025? This question is at the forefront as industries rapidly adopt new technologies, transforming traditional roles and creating demand for a skilled workforce.
Understanding Manufacturing Automation in the US
Manufacturing automation is transforming the U.S. industrial landscape. This involves integrating advanced technologies to enhance production efficiency, reduce costs, and improve product quality. But what exactly does this transformation entail, and why is it projected to accelerate significantly by 2025?
Current Trends in Automation
Automation is not a new concept, but its current iteration is far more sophisticated. We’re seeing increasing use of robotics, artificial intelligence (AI), and machine learning to perform tasks previously done by humans.
These trends are driven by several factors, including:
- Increased global competition
- The need for greater efficiency
- Advancements in technology
- Rising labor costs
The adoption of automation technologies varies across different manufacturing sectors. Industries such as automotive, electronics, and food processing have been early adopters due to their high production volumes and repetitive tasks.
Projected Growth of Automation by 2025
The projected 12% increase in manufacturing automation by 2025 indicates a significant acceleration. This growth is driven by factors such as the increasing affordability of automation technologies and the growing need for resilience in supply chains.
Areas expected to see the most growth include:
- Robotics and cobots (collaborative robots)
- AI-powered process optimization
- Predictive maintenance systems
- Automated quality control
Understanding the current trends and projected growth of manufacturing automation provides a foundation for exploring its potential impact on job creation. While automation can lead to increased efficiency and productivity, it also raises concerns about job displacement and the need for workforce adaptation.
The Initial Impact on Job Displacement
One of the primary concerns surrounding manufacturing automation is its potential to displace workers in existing roles. As machines and robots become more capable of performing tasks previously done by humans, some jobs inevitably become redundant. But what are the specific areas most at risk, and what strategies can mitigate these negative impacts?
Jobs Most Vulnerable to Automation
Certain types of jobs are more susceptible to automation than others. These typically include:
- Repetitive manual labor
- Assembly line positions
- Quality control inspectors (where AI-powered systems can perform inspections more accurately)
- Machine operators (as machines become more autonomous)
The displacement of workers in these roles can have significant economic and social consequences, particularly in regions heavily dependent on manufacturing.
Case Studies of Automation-Related Job Losses
Several case studies illustrate the impact of automation on job displacement. For example, the automotive industry has seen significant job losses due to the increased use of robotics in assembly lines.
Another example can be found in the electronics manufacturing sector, where automation has reduced the need for manual labor in tasks such as soldering and component placement.
These case studies highlight the need for proactive measures to address job displacement, such as retraining programs and support for affected workers.
Strategies for Mitigating Job Displacement
While automation can lead to job displacement, it doesn’t necessarily mean a net loss of jobs. By implementing strategic initiatives, manufacturers and policymakers can mitigate the negative impacts and create new opportunities.
These strategies include:
- Investing in retraining programs to equip workers with the skills needed for new roles
- Encouraging the development of new industries and technologies that create jobs
- Providing support for displaced workers, such as unemployment benefits and job placement assistance
Addressing the initial impact of automation on job displacement requires a comprehensive and proactive approach. By understanding the specific jobs at risk and implementing strategies to mitigate negative impacts, we can ensure a more equitable transition to a highly automated manufacturing sector.
New Job Creation Through Automation
While automation leads to job displacement in certain areas, it also creates new opportunities in other fields. The development, implementation, and maintenance of automation technologies require new skills and expertise, leading to the creation of new types of jobs. What are these new roles, and how can the workforce prepare for them?
Emerging Roles in Automation
The rise of manufacturing automation is creating demand for a skilled workforce in areas such as:
- Robotics engineering: Designing, building, and maintaining robots and automated systems
- Data science: Analyzing data generated by automated systems to optimize performance and identify areas for improvement
- AI development: Creating and implementing AI-powered solutions for manufacturing processes
- Automation technicians: Installing, troubleshooting, and repairing automated equipment
These emerging roles require a combination of technical skills, problem-solving abilities, and creativity.
Skills and Training Required
To take advantage of these new opportunities, workers need to acquire the necessary skills and training. This includes:
- STEM education: Focusing on science, technology, engineering, and mathematics
- Vocational training: Providing hands-on experience with automated equipment and technologies
- Continuous learning: Staying up-to-date with the latest advancements in automation
Educational institutions and training providers need to adapt their programs to meet the evolving needs of the manufacturing sector.
Examples of Companies Creating New Jobs
Several companies are already creating new jobs as a result of automation. For example, robotics manufacturers are hiring engineers and technicians to design, build, and support their products.
Software companies are also creating jobs in the development of AI-powered solutions for manufacturing optimization. These companies are investing in training programs to equip their employees with the necessary skills.
By focusing on new job creation and providing the necessary skills and training, we can ensure that the benefits of automation are shared broadly.
The Impact on the Skills Gap
One of the significant challenges in the context of manufacturing automation is the growing skills gap. As technology advances rapidly, the demand for workers with the right skills is increasing, while the supply of qualified candidates is not keeping pace. How can we bridge this gap to ensure that the workforce is prepared for the future of manufacturing?
Defining the Skills Gap
The skills gap refers to the mismatch between the skills that employers need and the skills that job seekers possess. This can manifest in several ways:
- Lack of technical skills: Insufficient knowledge of robotics, AI, and data science
- Soft skills deficit: Poor communication, problem-solving, and teamwork abilities
- Lack of experience: Insufficient hands-on experience with automated equipment
Addressing the skills gap requires a multi-faceted approach involving education, training, and collaboration between industry and academia.
Causes of the Skills Gap
Several factors contribute to the skills gap in manufacturing:
- Rapid technological advancements: The pace of change makes it difficult for educational institutions to keep up
- Aging workforce: Many skilled workers are retiring, taking their knowledge and experience with them
- Negative perceptions of manufacturing: Some people view manufacturing as a low-paying, unglamorous career
Addressing these underlying causes is essential for closing the skills gap.
Strategies for Closing the Skills Gap
To close the skills gap and prepare the workforce for the future of manufacturing, we need to implement the following strategies:
- Invest in STEM education: Encourage students to pursue careers in science, technology, engineering, and mathematics
- Strengthen vocational training programs: Provide hands-on experience with automated equipment and technologies
- Foster collaboration between industry and academia: Ensure that educational programs are aligned with the needs of employers
- Promote continuous learning: Encourage workers to stay up-to-date with the latest advancements in automation
By addressing the skills gap, we can unlock the full potential of manufacturing automation and ensure that the benefits are shared broadly across society.
The Role of Government Policies
Government policies play a crucial role in shaping the impact of manufacturing automation on job creation. By implementing policies that support workforce development, innovation, and economic growth, governments can help ensure a smooth transition to a highly automated manufacturing sector. What are some effective policies that can facilitate this transition?
Incentives for Automation Adoption
Government policies can encourage the adoption of automation technologies by providing financial incentives such as tax credits, grants, and loans. These incentives can help manufacturers invest in automation, which can lead to increased efficiency and productivity.
However, these incentives should be carefully designed to ensure that they do not exacerbate job displacement. For example, incentives could be tied to commitments to retraining and upskilling workers.
Investing in Education and Training
One of the most effective ways to mitigate the negative impacts of automation is to invest in education and training. Government policies can support the development of vocational training programs, apprenticeships, and other initiatives that equip workers with the skills they need for new jobs.
These programs should be aligned with the needs of employers and should focus on skills that are in high demand, such as robotics, AI, and data science.
Supporting Displaced Workers
Government policies can also provide support for workers who are displaced by automation. This can include unemployment benefits, job placement assistance, and retraining opportunities.
These support programs should be designed to help workers transition to new jobs as quickly and effectively as possible.
Promoting Innovation and Entrepreneurship
Finally, government policies can promote innovation and entrepreneurship by supporting research and development, providing access to capital, and reducing regulatory burdens.
These policies can help create new industries and technologies that create jobs, offsetting the job losses caused by automation.
Future Outlook and Recommendations
Looking ahead, the integration of automation in US manufacturing is poised to accelerate further. While some jobs may be displaced, strategic initiatives focused on workforce training, technological innovation, and supportive government policies can foster a balanced outcome. What key strategies should be prioritized?
Predictions for 2025 and Beyond
By 2025, we can expect to see:
- More widespread adoption of AI and machine learning in manufacturing
- Increased use of collaborative robots (cobots) that work alongside humans
- Greater emphasis on data analytics and predictive maintenance
- A growing demand for workers with advanced technical skills
These trends will require manufacturers to adapt their business models and invest in workforce development.
Recommendations for Businesses
To succeed in the age of automation, businesses should:
- Invest in workforce training and upskilling
- Embrace new technologies and business models
- Foster a culture of innovation and continuous improvement
- Collaborate with educational institutions and government agencies
Recommendations for Workers
To thrive in the changing job market, workers should:
- Acquire new skills and knowledge
- Be open to learning new technologies
- Develop strong problem-solving and critical-thinking abilities
- Embrace continuous learning and professional development
Final Thoughts
The projected 12% increase in US manufacturing automation by 2025 presents both challenges and opportunities. By proactively addressing the potential negative impacts and embracing the opportunities for new job creation, we can ensure that automation benefits all members of society.
Key Point | Brief Description |
---|---|
🤖 Automation Growth | Projected to increase by 12% by 2025, driven by technology and competition. |
💼 Job Displacement | Repetitive manual labor and some machine operation roles are most at risk. |
🌱 New Job Creation | Emerging roles in robotics, AI, data science, and automation maintenance. |
🎓 Skills Gap | Mismatch between employer needs and worker skills requires STEM education and training. |
FAQ
▼
Automation may displace some jobs, particularly those involving repetitive manual tasks. However, it also creates new jobs related to designing, implementing, and maintaining automated systems, requiring a shift in workforce skills.
▼
Skills related to robotics, AI, data science, and automation maintenance are highly sought after. Workers need to be proficient in programming, troubleshooting, and data analysis to manage and optimize automated systems.
▼
Companies can invest in workforce training and upskilling programs to equip employees with the necessary skills. They should also foster a culture of innovation and be open to embracing new technologies and business models.
▼
Government can offer incentives for automation adoption tied to worker retraining, support displaced workers with benefits and job placement, and invest in STEM education to prepare future generations for technology jobs.
▼
Workers should focus on acquiring new skills relevant to automation, such as programming and data analysis. They should also embrace continuous learning and be open to adapting to new roles and responsibilities in the evolving workplace.
Conclusion
The anticipated 12% surge in US manufacturing automation by 2025 necessitates a proactive and balanced strategy, focusing on mitigating job displacement through comprehensive training and fostering innovation to generate new employment opportunities. This approach ensures the benefits of automation are widely shared.